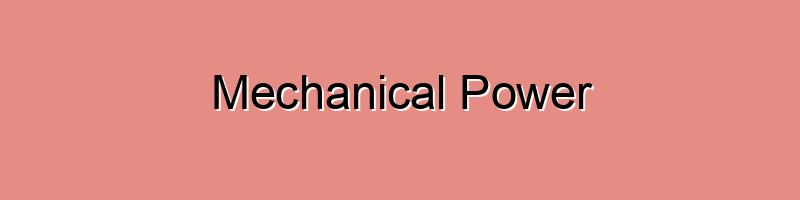
Mechanical power refers to the ability of a machine or mechanical system to perform work or exert force. In simpler terms, it’s the energy produced by moving parts, like engines or motors, to do something useful, such as moving objects or generating electricity.
Types:
- Electric Power: Generated by electric motors or generators.
- Hydraulic Power: Uses fluid pressure to generate force.
- Pneumatic Power: Utilizes compressed air to produce mechanical motion.
Causes:
- Friction: Increased friction between moving parts can hinder mechanical power.
- Wear and Tear: Over time, components can degrade, reducing efficiency.
- Lubrication Issues: Insufficient or improper lubrication can lead to mechanical issues.
- Misalignment: Parts not properly aligned can cause strain and reduce power.
- Overloading: Putting excessive strain on the system can lead to breakdowns.
- Temperature Changes: Extreme temperatures can affect materials and performance.
- Corrosion: Damage from rust or corrosion can weaken components.
- Poor Maintenance: Neglecting regular upkeep can cause deterioration.
- Design Flaws: Inadequate design may lead to inefficiencies or failures.
- External Forces: Impact from external factors like accidents or natural disasters.
- Power Supply Issues: Interruptions or fluctuations in power sources.
- Material Defects: Inferior materials may lead to premature failure.
- Vibration: Excessive vibration can cause damage over time.
- Environmental Conditions: Exposure to harsh environments can degrade performance.
- Age: Older machinery may naturally lose efficiency.
- Inadequate Training: Improper use or operation can cause damage.
- Imbalance: Uneven distribution of weight or force can affect performance.
- Clogging or Blockages: Obstructions can impede movement or flow.
- Electrical Issues: Malfunctions in electrical components can disrupt power.
- Manufacturing Defects: Flaws introduced during production can impact performance.
Symptoms:
- Reduced Efficiency: Decreased output compared to normal operation.
- Increased Noise: Unusual sounds during operation can indicate problems.
- Vibration: Excessive shaking or vibration during use.
- Overheating: Elevated temperatures beyond normal operating range.
- Frequent Breakdowns: More frequent malfunctions or failures.
- Strange Odors: Unusual smells like burning rubber or oil.
- Leaking Fluids: Fluids such as oil or coolant leaking from the system.
- Uneven Movement: Jerky or uneven motion during operation.
- Visible Damage: Physical damage or wear on components.
- Irregular Operation: Inconsistent performance or operation.
- Loss of Power: Decreased force or ability to perform work.
- Difficulty Starting: Trouble initiating operation or power-up.
- Excessive Friction: Increased resistance during movement.
- Erratic Behavior: Unpredictable operation or response.
- Smoke: Smoke emanating from the system during use.
- Warning Lights: Illumination of warning indicators or lights.
- Stalling: Unexpected halting of movement or operation.
- Dragging: Components or parts dragging during use.
- Electrical Issues: Flickering lights or electrical malfunctions.
- Unusual Vibrations: Vibrations outside of normal parameters.
Diagnostic Tests
(History, Physical Examinations):
- History Taking: Gathering information about the machine’s usage, maintenance history, and any recent incidents or changes.
- Visual Inspection: Examining the machine for visible damage, leaks, or irregularities.
- Functional Testing: Running the machine through various operations to observe performance.
- Vibration Analysis: Using specialized tools to measure and analyze vibration patterns.
- Thermographic Imaging: Checking for temperature anomalies using infrared imaging.
- Fluid Analysis: Examining fluids such as oil or coolant for contaminants or signs of wear.
- Electrical Testing: Checking electrical components for proper function and continuity.
- Load Testing: Applying varying loads to assess performance under different conditions.
- Alignment Checks: Verifying proper alignment of components using precision instruments.
- Noise Analysis: Listening for unusual sounds and identifying their sources.
- Computer Diagnostics: Utilizing software and sensors to monitor performance parameters.
- Torque Measurement: Measuring torque output to assess mechanical power.
- Pressure Testing: Checking fluid or air pressure levels within the system.
- Component Disassembly: Disassembling parts for closer inspection and measurement.
- Comparative Analysis: Comparing current performance metrics to established benchmarks.
- Stress Analysis: Assessing structural integrity and stress points.
- Historical Data Review: Analyzing past performance data for trends or anomalies.
- Endoscopic Inspection: Using cameras to inspect internal components without disassembly.
- Dynamic Balancing: Balancing rotating components to reduce vibration and wear.
- Consultation with Experts: Seeking input from specialists or engineers for complex issues.
Treatments
(Non-Pharmacological):
- Regular Maintenance: Implementing a schedule for lubrication, cleaning, and inspection.
- Proper Lubrication: Ensuring the correct type and amount of lubricant for moving parts.
- Component Replacement: Swapping out worn or damaged parts with new ones.
- Alignment Adjustment: Aligning misaligned components to reduce strain.
- Temperature Control: Installing cooling or insulation measures to regulate temperature.
- Training Programs: Providing education for operators on proper usage and maintenance.
- Upgrades and Retrofits: Installing newer, more efficient components or systems.
- Environmental Controls: Shielding machinery from harsh weather or contaminants.
- Vibration Dampening: Installing vibration-absorbing materials or mounts.
- Safety Measures: Implementing safeguards to prevent accidents or damage.
- Load Management: Reducing excessive loads to prevent strain on the system.
- Root Cause Analysis: Investigating underlying issues to prevent recurrence.
- Emergency Protocols: Establishing procedures for handling breakdowns or failures.
- Inspection Checklists: Creating standardized checklists for routine inspections.
- Operator Feedback: Encouraging operators to report anomalies or concerns promptly.
- Quality Control Measures: Ensuring proper manufacturing standards are met.
- Energy Efficiency Programs: Optimizing energy usage to reduce strain on systems.
- Contingency Plans: Planning for contingencies such as power outages or malfunctions.
- Remote Monitoring: Implementing systems to monitor performance remotely.
- Continuous Improvement: Seeking ongoing refinements to enhance efficiency and reliability.
Drugs:
(Mechanical power issues typically do not involve pharmaceutical intervention. However, lubricants and additives may be considered in specific cases.)
Surgeries:
- Component Replacement Surgery: Removing and replacing worn or damaged parts surgically.
- Alignment Surgery: Surgical correction of misaligned components.
- Reconstruction: Rebuilding damaged or degraded components.
- Clearing Blockages: Surgical intervention to remove obstructions or blockages.
- Repair of Structural Damage: Surgical repair of structural integrity compromised by damage.
- Implantation of Enhancements: Adding aftermarket enhancements or upgrades.
- Reinforcement Surgery: Strengthening weak or vulnerable areas.
- Revision Surgery: Corrective surgery following failed previous interventions.
- Balancing Procedures: Surgical adjustment to balance rotating components.
- Custom Fabrication: Designing and fabricating custom components or solutions.
Preventions:
- Regular Maintenance: Scheduled checks and upkeep to catch issues early.
- Proper Training: Thorough training for operators on usage and maintenance.
- Quality Materials: Using high-quality materials in manufacturing and maintenance.
- Design Reviews: Comprehensive reviews to identify and address potential flaws.
- Environmental Controls: Protecting machinery from harsh environments.
- Safety Protocols: Implementing safety measures to prevent accidents.
- Monitoring Systems: Installing sensors and monitors to detect problems early.
- Contingency Planning: Having plans in place for emergencies or failures.
- Upgrades and Retrofits: Updating systems with newer, more reliable components.
- Documentation: Maintaining detailed records of maintenance and repairs.
When to See Doctors:
- Persistent Issues: If mechanical power problems persist despite attempts at troubleshooting and maintenance.
- Safety Concerns: If there are safety hazards associated with the malfunctioning machinery.
- Sudden Changes: If there are sudden and significant changes in performance or operation.
- Unusual Noises or Smells: If there are unusual sounds or smells emanating from the machinery.
- Visible Damage: If there is visible damage or wear on critical components.
- Frequent Breakdowns: If breakdowns or failures occur frequently despite regular maintenance.
- Loss of Efficiency: If there is a noticeable decrease in efficiency or output.
- Overheating: If the machinery is overheating beyond normal operating temperatures.
- Vibration or Shaking: If there is excessive vibration or shaking during operation.
- Electrical Issues: If there are electrical malfunctions or anomalies.
Disclaimer: Each person’s journey is unique, treatment plan, life style, food habit, hormonal condition, immune system, chronic disease condition, geological location, weather and previous medical history is also unique. So always seek the best advice from a qualified medical professional or health care provider before trying any treatments to ensure to find out the best plan for you. This guide is for general information and educational purposes only. If you or someone are suffering from this disease condition bookmark this website or share with someone who might find it useful! Boost your knowledge and stay ahead in your health journey. Thank you for giving your valuable time to read the article.